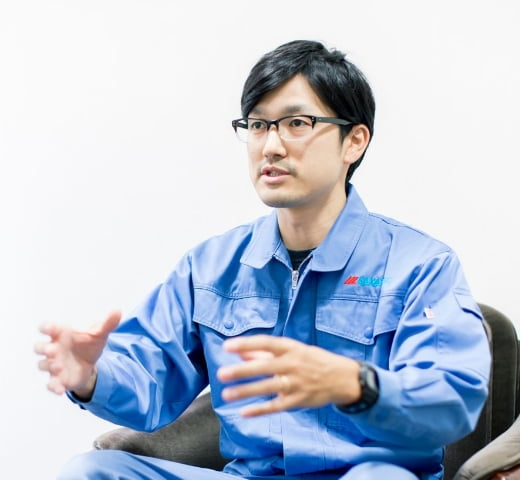
いつ起きるかわからないトラブルを
「その場で何とかする」醍醐味
お客様のものづくりに欠かせない付帯設備を、トータルにサポート――。それがサービス部門の担う役割です。計量混合機に乾燥機、温調機。新しい納入機器の据付は配管・配線工事、試運転にチェック、取扱の説明。定期的な点検・メンテナンスでは、消耗・劣化した部品の修理・交換。そして、緊急トラブルへの対応や設備の改善提案まで。幅広く多面的に樹脂成形工場の安心・安定の稼働を支えています。特に、故障修理の依頼はいつ起きるかわかりません。できる限り早く安く「その場で何とかする」のが、サービスマンの腕の見せどころですし醍醐味です。ただ、敢えて応急措置だけに留めることもあります。老朽化が原因なら、部分的に修理するよりも、いいタイミングで機器を一新した方が、長期的に見て安心して使い続けることができますから。「一人前になれたかな」と感じたのは5年目ぐらいですが、いつも「もっと、こうできたかも…」という想いは残りますし、それが成長へのモチベーションにもなっています。
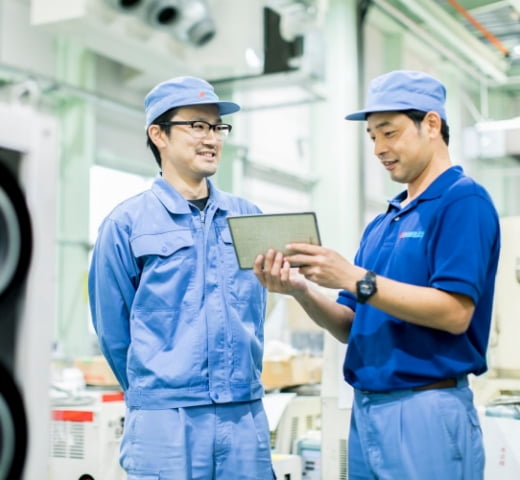
100社あれば100通りの工場を
止めることなく、説得力ある仕事をする
サービスマンとしての誇りは、修理やメンテナンスのためだけに工場を止めないことです。操業が止まる休日など限られた時間の中でやり遂げるために、営業や設計にも相談しアドバイスももらいながら、しっかりと手順を組んでいきます。お客様の工場は材料も製品も、生産管理の仕方も、100社あれば100通り。材料が硬いと、金属が削れたり静電気が起きてへばりついたり。トラブルの原因も様々で突き止めていくのは難しいですが、心がけているのはお客様に対して説得力を持つこと。最善を尽くしても、いいと思って提案したことも、納得できる知識と話のわかりやすさがなければうまく伝わりません。サービスマンは機器に触れる仕事ですが、それ以上にお客様の心に触れて、信頼を築くコミュニケーション力が大事ですね。どんな状況なのか、何をしてどういう結果になったか、どんな要望を受けたか。1件ごとに作成するサービスレポートはデータベース化し、全社で誰もが見られるようになっています。他のサービスマンの仕事から学んで成長できますし、設計の商品開発や営業提案にも活かししてもらえれば嬉しいです。
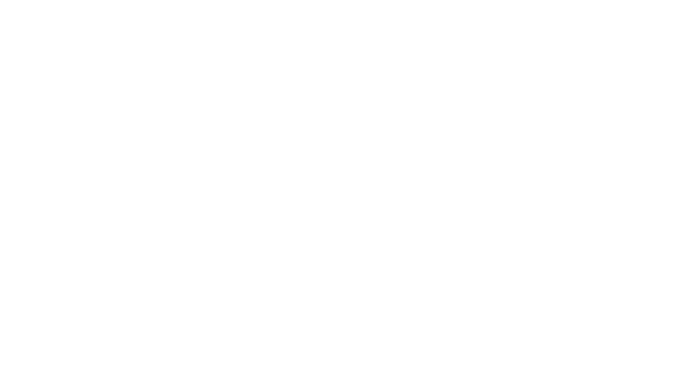
ワタシの“解決”エピソード
「それよりも、こう修理した方がいいですよ」と提案することも少なくありません。お客様の意向や選択肢は間違いじゃない。でも、メインの樹脂成形機と付帯設備、多くの機器が一つの流れになってプラスチック製品が生まれるなかで、その一部だけを見ていることが多いです。据付工事では、この機器は1階に、それは2階に、ここの壁をぶち抜いて…、というお客様の計画を、その場で「こういうレイアウトの方がムダなく、人も動きやすいですよ」と提案し、変更したこともありました。現場で接する生産管理担当の方々に、全体像を俯瞰して考えてもらえるように「お客様になりきる」ぐらいの気持ちでいると、使い勝手のより良い姿が見えてきます。それがサービスマンという仕事だと感じています。
1DAY
SCHEDULE
ある1日の流れ
移動中の車内は、仕事の段取りはもちろん、誰にも邪魔されずにいろんな考え事を巡らせる、貴重な時間です。スケジューリングを任せてもらえるのも嬉しいですね
山奥があれば、海沿いも。いろんな地域へ足を運ぶので、その土地の名物料理を味わうのが楽しみです
現場に駆けつけ、まずは何がどうなっているのか、自分の眼で見て診断します。状況をヒアリングしてお客様と情報を共有し、様々な可能性から原因を切り分け、具体的にどう修理するか、対処策の選択肢を提案しています
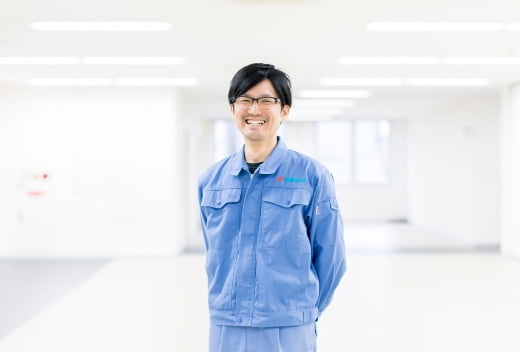
MY REASON カワタを選んだ理由
扱う機器の種類も、訪問するお客様の業界も幅広く、いろんな経験や知識が得られるのが魅力でした。やるべきことが最初から決まっていることは少なく、修理の方法は本当にさまざま。機器の据付では、設備工事や電気工事などの専門家が揃う現場の指揮官にもなるので、人を動かす幅広い知識とコミュニケーション力が求められます。法律が変わればその都度、対応も必要ですが、そうした新しいことを一つずつ身に着けていく充実感が味わえる仕事ですね。業界のパイオニアであるカワタのブランド力も日々、実感しています。プラスチック成形業界は横のつながりが強いので、「いい評判、聞いたよ」と、遠回りに評価の声を耳にすることも多いです。
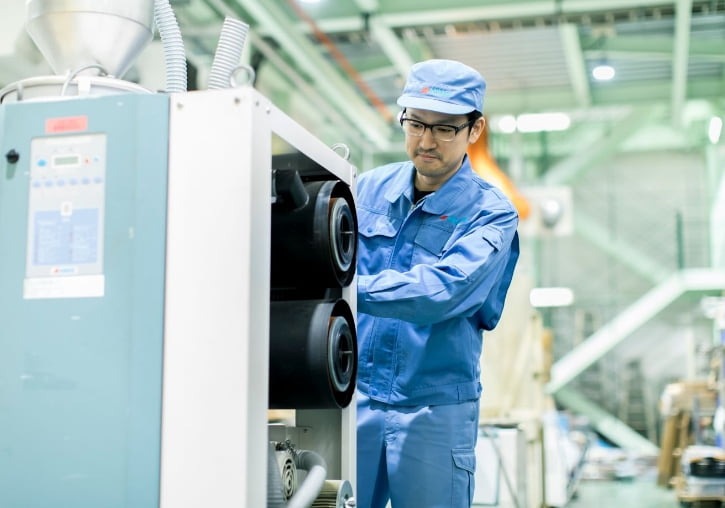
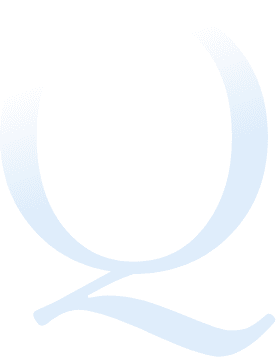
これからチャレンジしたいこと
運ぶ、計る、混ぜる、乾かす、温調する、砕く…。工程のすべてを理解し、その流れがスムーズになって、お客様が楽になる設備サポートとご提案を、もっともっとしていきたいですね。どんどん新しい機器が開発され、お客様の現場も高度化、小型化し、さらに最先端のIoTへと変わっていきます。人の手でやっていた作業を機械化し、産業機器の利活用が進むほど、サポートするサービスマンの重要性は高まります。サービス履歴やデータを蓄積し、トレースできるようになって、より早く的確な仕事が可能になり、お客様の説得力も高めていけるのが楽しみです。将来は、サービスマンを束ねるリーダーにもなっていきたいですね。